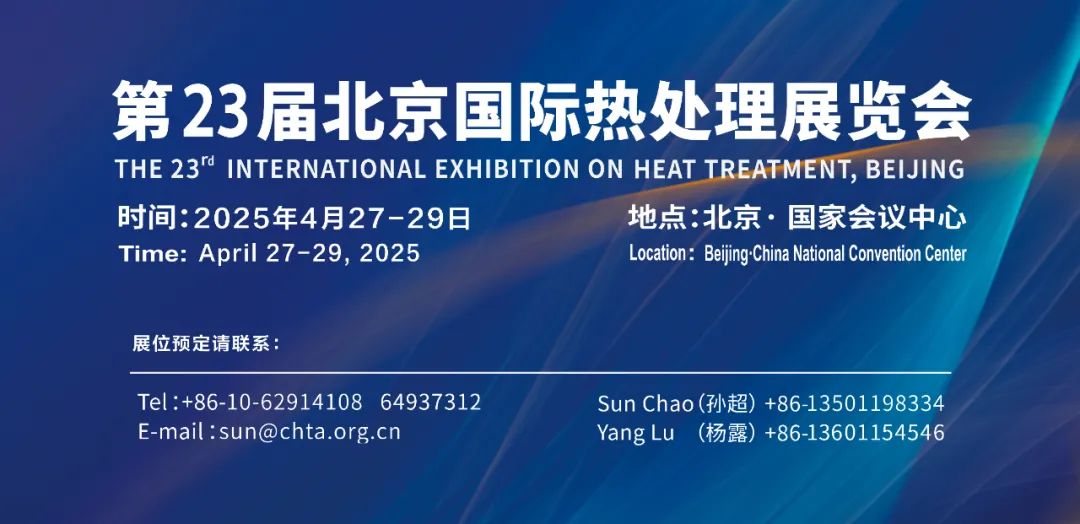
马氏体相变是材料科学与工程领域的重要基础理论,是钢铁材料热处理强化的主要手段。控制马氏体相变过程中,压力、温度和化学成分均为重要的热力学变量,对马氏体相变有较大影响。尤其是压力达到GPa 级时,可以在不改变化学成分的前提下影响马氏体相变的动力学和热力学。目前,国内外关于钢铁材料高压淬火已有一些初步研究。ZHANG H W和陈鑫等报道了高压诱发工业纯铁在低于10℃/s 冷却速率下即可发生马氏体相变获得细板条马氏体。CUI Q 等研究了高压(3~5GPa)淬火对工业纯铁马氏体相变机制及力学性能影响。结果表明,5GPa压力下淬火,其板条马氏体间多呈{112}[111]孪晶对称关系,拉伸强度达700 MPa,并维持良好塑性(伸长率为27%)。WANG ZH 等研究了高压(1~5GPa)淬火对IF 钢组织和硬度的影响。结果表明,IF 钢高压淬火后获得了典型板条马氏体组织,马氏体板条厚度从微米级减小至纳米级;5GPa 下Block 板条束被细化至19nm,硬度高达780HV,接近常压高碳钢淬火水平。CUI Q等研究了4GPa压力下20钢淬火马氏体精细结构及性能。
结果表明,高压淬火马氏体板条宽度为20~250nm,其硬度为654HV,较常规淬火提高70.39%。SUN HD 等研究了高压(1~6 GPa)淬火对45 钢板条马氏体晶格内过饱和碳含量的影响。结果表明,马氏体晶格内固溶碳质量分数w(C)与压力(P)关系为:w(C)=0.09+0.06P;固溶强化(σs)与过饱和碳质量分数的平方根成正比:σs=1400+2779 w(C)1/2。CUI Q 等研究了3GPa 淬火对40Cr 钢马氏体组织及力学性能影响。结果表明,3GPa 高压下淬火后40Cr 钢淬火组织中片状马氏体含量远高于常规淬火,原奥氏体晶粒(PAG)尺寸细化至15μm,且基体上弥散分布着大量合金渗碳体;硬度(807HV)较常规淬火提高40%,压缩屈服强度高达3.5 GPa,是常规淬火的3 倍。可见,在GPa 级压力作用下淬火,对Fe-C 合金马氏体相变及其力学性能有着深刻的影响,但研究对象局限于IF 钢、工业纯铁、以及20 和45 钢等,且仅研究高压淬火马氏体组织形态,对淬火压力与马氏体晶体结构及组织形态相关性等尚缺乏系统性研究。
为此,本文以35钢作为研究对象,系统研究淬火压力(2~4GPa)对35钢马氏体精细结构(晶体结构、马氏体类型、碳原子分布有序度、位错及孪晶密度等)以及马氏体组织细化程度等的影响,研究淬火压力对35 钢力学性能的影响,探讨高压淬火马氏体精细结构与力学性能间的相关性,揭示高压淬火马氏体力学性能提升机制。
试验材料为退火态35钢,化学成分(质量分数,%)为:0.32~0.40C,0.17~0.37Si,0.50~0.80Mn,w(S)≤0.035,w(P)≤0.035,w(Cr)≤0.25,w(Ni)≤0.25,w(Cu)≤0.25,余量Fe。采用电火花线切割将其加工成直径6mm、高8mm 的小圆柱试样,用于高压淬火试验。采用CS-1V 型六面顶液压机进行高压淬火试验。图1 所示分别为高压试验工作原理和高压样品组装套示意。首先按照原始试样尺寸,机加工出相应尺寸的氮化硼坩埚(外径10mm,内径6mm,高度8mm)和实心氮化硼垫片(10mm×6mm)。先将氮化硼、叶腊石、导电钢圈、墨坩埚等部件在烘干箱进行充分烘干,然后将合金试样及其组件按照图1(b)示意进行装配,再放入六面顶液压机的6个锤头中间位置,如图1(a)所示。在组装过程中,通过叶腊石直角处钻出的小孔将K 型热电偶伸入叶腊石内部,使其与试样接触,并将热电偶的另一端连接到测温设备上。利用六面锤头分别从3个方向通过液压驱动共同挤压立方体腔体,实现GPa 级压力的提升。设定淬火压力分别为2、3 和4GPa,保持压力下升温至预设的奥氏体化温度,保温20min。之后保持压力以6℃/s 的冷却速率冷却至室温(淬火)。试验时使用K 型热电偶测量温度。
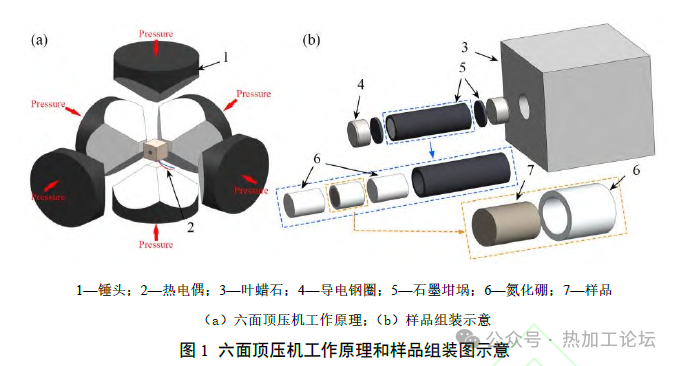
35钢高压淬火下奥氏体化温度确定方法如图2 所示(以2GPa 为例)。2GPa 高压下,在710~920 ℃温度区间对35钢进行加热(保温20 min),保压下冷却至室温,然后分别测试冷却后试验合金的硬度(图2),并根据淬火样品XRD 图谱采用标准样品法[15]以及淬火组织观察定量分析马氏体含量,确定最佳奥氏体化温度为860 °C。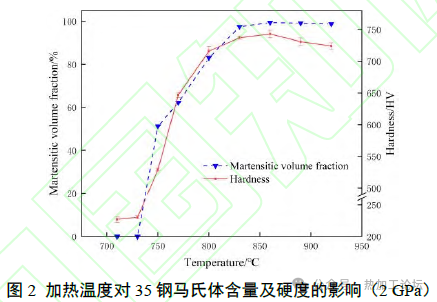
采用Axio Scope A1 Pol 光学显微镜(OM)和ZEISS SUPRA 55 扫描电子显微镜(SEM)对显微组织进行观察分析。利用D/max-2500/PC 型X 射线衍射仪(XRD)对处理后的样品进行结构分析,获得样品相组成及晶格常数等信息,试验条件为:采用Cu-Kα 辐射,试验电压20 kV,扫描步长0.4°。 利用SUPRA-55 型扫描电镜附带的TSL OIM EBSD 系统采集EBSD 数据,并用Channel 5 分析软件获取马氏体组织结构特征,扫描步长为0.2 μm,工作电压为20 kV。EBSD 样品制备:将砂纸打磨至表面光洁的样品在-10℃下置于10%的高氯酸酒精溶液中进行电解抛光(电压为20 V,电解时间为20~30 s)。晶界分布图中,小角度晶界(取向差角小于15°)为绿色线,大角度晶界为黑色线,60°[111]孪晶界为红色线,60°[011]晶界为黄色线,49.5°[011]晶界为蓝色线。 利用Tecnai G2 F20 透射电子显微镜(TEM)观察马氏体精细结构。TEM 样品制备:直径3 mm 薄片样品打磨至30~50 μm 后,在-20℃下进行电解双喷,双喷液为10%的高氯酸酒精溶液。利用德国wissel 穆斯堡尔谱仪在室温下以等加速方式测量了M?ssbauer 光谱,测试时,使用Rh 基体中的57Co 源,用多个?-Fe 膜样品进行标定。 在HV-1000A 硬度计上测量硬度,载荷为49 N,每种样品的最终硬度值为5 次测量的平均值。压缩试验采用WDW3100 微机控制电子万能试验机(附带Inspekt-Table 力学测试系统)测试,设定压下速率为0.5 mm/min,最大压力为90000 N,每种状态的合金选取3 个样品进行测试并取平均值。 图3所示为初始退火态35 钢的组织(OM)。由图可知,35 钢原始组织由珠光体和铁素体构成,显微组织中珠光体和铁素体均很细小。在奥氏体冷却过程中,共析反应生成的珠光体一般在奥氏体晶界处形核。原奥氏体晶粒较小时晶界较多,所以珠光体的形核部位较多、形核率较高,室温下得到细小的珠光体和铁素体。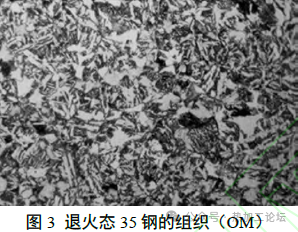
图4所示分别为常压及2、3、4 GPa 下35 钢淬火组织。与35 钢常规淬火获得的混合马氏体组织(图4(a))相比,2GPa 下淬火组织(图4(b))马氏体板条束结构特征、即板条-板条束-板条束群等级结构特征较为显著,马氏体板条束更细,片状马氏体分布于板条马氏体基体上,马氏体片宽度减小。3GPa 下淬火组织(图4(c))马氏体板条束结构特征更为显著,马氏体板条束密实度进一步提高,细长片状马氏体特征较为明显(如图4(c)中箭头所示)。而当淬火压力升至4GPa 几乎分辨不出马氏体形态特征,如图4(d)所示,即4GPa 高压淬火极大地细化了马氏体组织。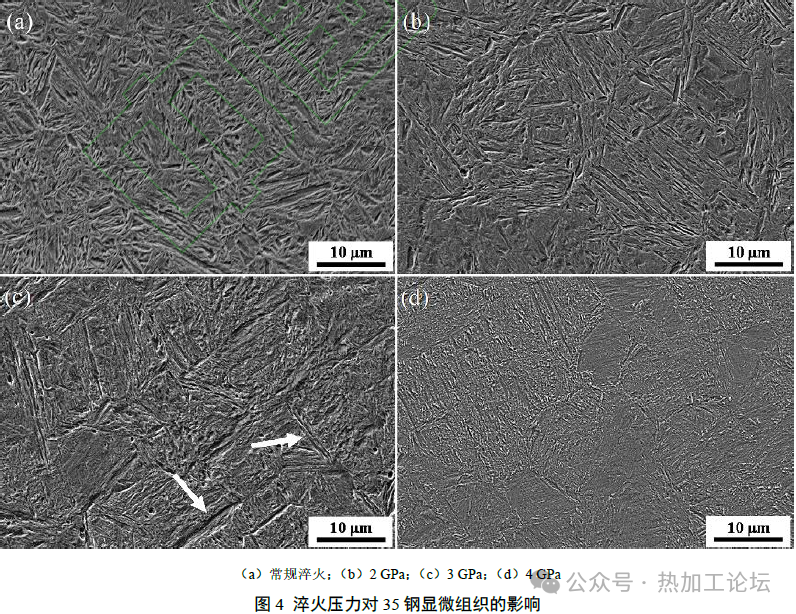
图5 所示为35 钢常规淬火组织的EBSD 分析结果。由图5(a)~(c)可知,35 钢常规淬火组织为典型的中碳钢淬火获得的混合马氏体组织,其片状马氏体(图5(b)中箭头)和板条状马氏体混杂分布,马氏体片与马氏体板条束具有不同的生长取向;1 个奥氏体晶粒内(图5(c))板条束与板条束之间取向相近,呈小角度晶界(取向差角小于15°,图5(d)中的绿色线);板条群间取向相差较大,呈大角度晶界(红色),马氏体板条束平均等效尺寸为1.89 μm。由图5(d)可知,淬火组织中存在60°[011]、49°[011]晶界以及60°[111]孪晶界。经计算,35 钢常规淬火组织中小角度晶界和60°[111]孪晶界所占比例分别为41%和6%。
图6 所示分别为2、3 和4 GPa 高压下35 钢淬火组织的EBSD 分析结果。2GPa 下淬火(图6(a)~(c))马氏体板条束结构特征更加明显,马氏体板条束宽度较常规淬火(图5(a))大幅细化,且同取向板条束尺寸增多。由于马氏体板条细化,且板条间分布着较高密度的小角度晶界和孪晶界,使得片状马氏体特征愈发明显,片状马氏体含量较常规淬火显著提高,且能清晰地观察到片状马氏体或形成于原始奥氏体晶界处(图6(a)中箭头A 所示)或分布于板条束间(图6(a)中箭头B 所示)。此外,与图5(d)对比可知,2 GPa 淬火组织中位错和孪晶等缺陷密度(图6(c))大幅提高。3GPa下淬火片状马氏体形貌特征明显(图6(d)中箭头A 所示),马氏体板条束愈加细化(图6(d)中箭头B 所示),分布于马氏体板条束上的小角度晶界及孪晶界密度(图6(f)所示)较2 GPa 下淬火进一步提高。当淬火压力升至4 GPa,如图6(g)~(i)所示,不仅马氏体板条更加细化,马氏体片也明显细化,单位面积上的位错密度和孪晶界密度较3 GPa 淬火增高。此外,如图6 所示,1 个原奥氏体晶粒(图6(e)和(h)中的晶粒D 和晶粒F)内马氏体板条束取向更加一致。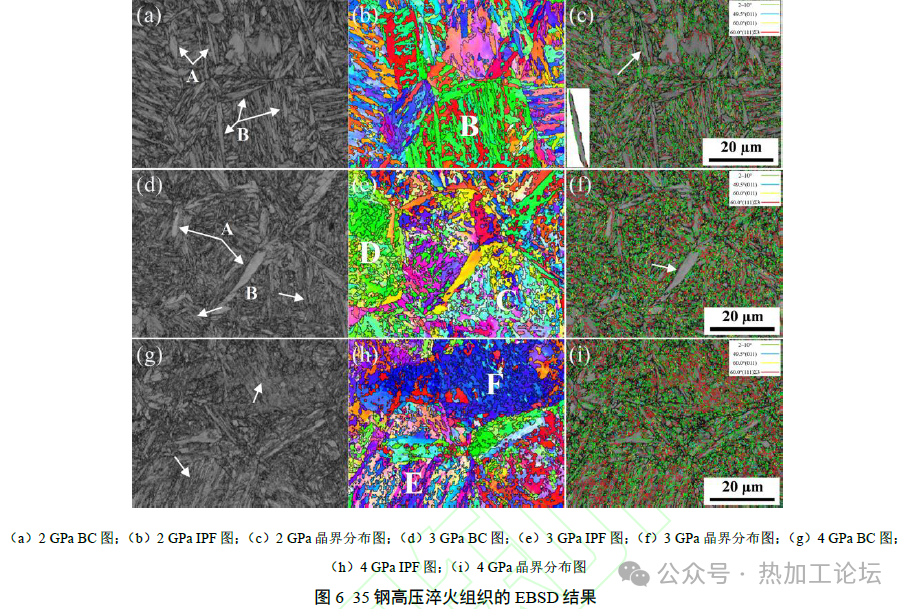
Ms 点温度(奥氏体向马氏体转变温度)通常由过冷奥氏体中固溶碳含量所决定。35钢在常压下的Ms温度接近359 ℃。FUJITA M 等[18]研究发现,压力会降低含Fe-C 合金的Ms 温度,压力每提高1GPa,其Ms 点温度约降低40 ℃。由此可求得2、3 和4GPa 下35钢的Ms 点温度分别为279、239、199 ℃,且Ms 点温度分别与常压下60、70 和95 钢的Ms 点温度相近,片状马氏体含量随淬火压力的升高逐渐增加。 图7所示为35 钢常规及2、3、4 GPa高压淬火组织中大小角度晶界所占比例。经分析,常规及2、3、4 GPa 淬火组织中,小角度晶界(LAGB)所占比例分别为41%及38%、34%、33%,60°[111]孪晶界所占比例分别为6%及17%、21%、26%,即随淬火压力升高,淬火组织中60°[111]孪晶界所占比例提升。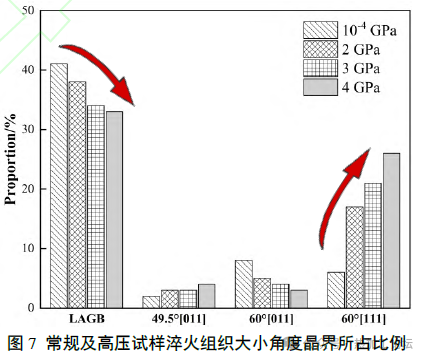
图8 所示为常规淬火及2、3、4 GPa 高压淬火35 钢1 个原奥氏体晶粒内的马氏体变体分布及其对应的(001)极图[分别对应图5 中晶粒A(常压)和图6 中晶粒B(2 GPa)、C(3 GPa)、E(4 GPa)]。经分析,常规淬火[图8(a)和图8(e)]及2 GPa[图8(b)和图8(f)]、3 GPa[图8(c)和图8(g)]、4GPa[图8(d)和图8(h)]淬火马氏体均有24 种变体,与相应的马氏体变体对,如V1-V2、V14-V17 等。V1-V2 是图8(c)中片状马氏体的变体对,孪晶取向为60°[111],并对照标准马氏体(001)极图,原奥氏体和马氏体间取向遵循K-S 关系。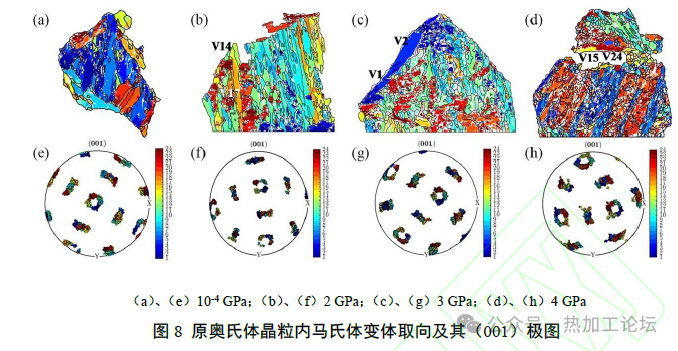
由上述SEM 和EBSD 结果可知,35 钢高压淬火组织最大特点是马氏体板条束细化及60°[111]孪晶界比例升高,因此利用TEM 进一步观察了高压2~4 GPa 淬火马氏体板条尺寸及精细结构,结果如图9 所示。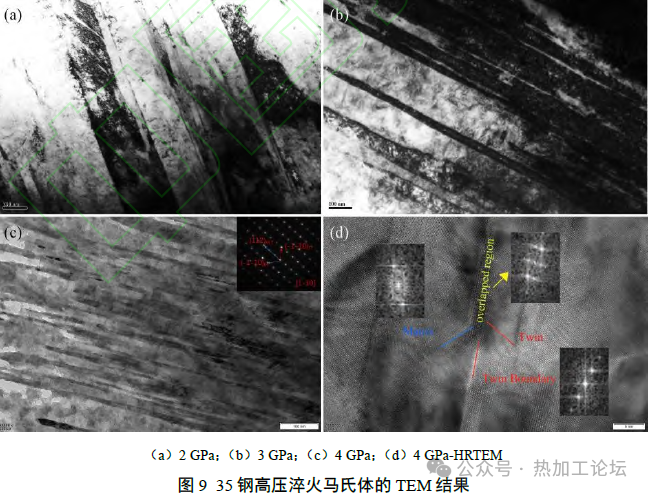
由图9(a)~(b)可知,2 GPa 和3 GPa 淬火时马氏体板条宽度分别为20~40 nm 和10~30 nm(利用DigitalMicrograph 软件测量并统计10 张板条马氏体的TEM 明场像);4 GPa 淬火时马氏体板条细化至5~15 nm,平均厚度约14 nm,如图9(c)~(d)所示。此外,对图9(c)中插图所示的衍射花样([11_0]晶带轴)进行标定可知,在高压淬火下两相邻马氏体变体间多遵循{112}[111]孪晶对称关系,因此,在4GPa 压力下淬火35 钢的显微组织中普遍存在{112}[111]孪晶对称板条。这也解释了高压淬火组织中60°[111]孪晶界面所占比例随淬火压力升高而增大。 图9(d)所示为4 GPa 样品中孪生结构的高分辨率TEM 图像。晶格条纹显示a-Fe 区域宽达几纳米,而孪生区域与基体重叠的孪生边界也有1~5 nm 厚。 综上所述,35 钢高压淬火组织主要特征:1)马氏体板条束显著细化,由常规淬火下的500 nm 逐渐细化至4 GPa 淬火下的14 nm;2)单位面积上位错密度大幅提高;3)呈60°[111]孪晶对称关系的板条马氏体变体对增多。 马氏体相变是替换原子无扩散(成分不改变,近邻原子关系不改变)和切变(母相和马氏体之间呈位向关系)而使其形状改变的相变。马氏体相变过程会产生很大的阻力,如界面能、面应变能、克服切变阻力以及马氏体中形成位错或孪晶亚结构所需的能量等。此外,奥氏体转变为马氏体时又会产生体积膨胀。而在GPa 级高压作用下淬火时,由于马氏体相变是在GPa 级压力下进行的,切变阻力以及结构畸变带来的晶格应变能及界面能都很高。系统为降低这些能量,会产生很多马氏体变体,马氏体变体将借助相互间的孪晶界面滑移,此时马氏体相变切变方式以孪晶为主,而非位错滑移,这些变体自动协调排列成能量较低的状态,生成较多的孪晶片状马氏体。 分别利用穆斯堡尔谱及XRD 研究了淬火压力对C 元素分布规律及马氏体晶界结构的影响。图10 所示为常规淬火和高压淬火35 钢的穆斯堡尔试验结果及拟合曲线。通过拟合光谱所计算的穆斯堡尔参数见表1。由图10 可知,常规和高压淬火35 钢的穆斯堡尔谱均由铁磁性相(马氏体)的非对称六线谱和顺磁性相(残余奥氏体或合金碳化物)在零速度附近的单峰(单线)穆斯堡尔谱谱线叠加而成,即常规及高压淬火35 钢的穆斯堡尔谱皆由马氏体和残余奥氏体(A0)的穆斯堡尔亚谱按权重叠加而成,其中超精细磁场为33.1T 和(30.5±0.1)T 的单峰分别为M2型马氏体(接近纯铁)和M3 型马氏体(第3 亚点阵,处于八面体间隙位置的碳原子作为近邻的铁原子组态)。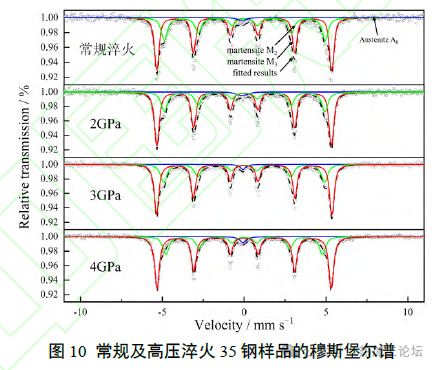
由表1 可知,常规淬火的35 钢中M2 和M3 型马氏体所占比例分别为63.59%和34.35%;2~4 GPa 高压淬火时,M2 和M3 型马氏体体积分数由2 GPa 淬火的65.50%和32.35%转变为4 GPa 淬火的72.93%和24.60%,即2~4 GPa 高压淬火马氏体碳分布有序度高于常规淬火,且随淬火压力增加而升高,但M3 型(第3 亚点阵)马氏体所占比例减少。此外,由表1 可知,35 钢高压淬火组织中残余奥氏体量较常规淬火略有增加,4 GPa 淬火组织中残余奥氏体量(2.47%)仅比常规淬火(2.06%)增加0.41个百分点。这可能是高压下淬火时马氏体形成带来的体积膨胀对未转变的奥氏体造成更大的压应力所致。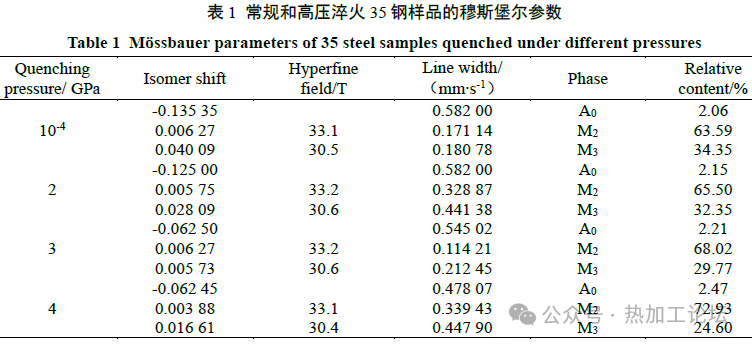
研究表明,间隙固溶碳原子的平衡浓度与压力的关系如式(1)所示。
式中:cp 为间隙固溶碳原子的平衡浓度;c0 为常数,mol/L;V 为摩尔体积变化,L/mol;R 为气体常数,L·kPa/(K·mol);Τ 为Ms 温度,K;P 为压力,GPa。 由式(1)可知,马氏体中间隙固溶原子平衡浓度随压力呈指数衰减,即随淬火压力升高,第三亚点阵的M3 型马氏体所占比例逐渐减少,M2 型马氏体逐渐增多,碳原子分布有序度逐渐提高。 图11所示为不同压力下淬火35 钢的XRD 图谱。根据(110)衍射峰信息,计算得到马氏体晶格常数,见表2。由表2 可知,马氏体的晶格常数a 和c 均随着淬火压力增高而降低,但晶格常数c 的降低幅度略小于a,导致马氏体正方度(c/a)逐渐增大,并由常规淬火的1.009 逐渐提升到4 GPa 的1.014,即2~4 GPa 下淬火提高了马氏体的正方度。由此进一步证实,高压下淬火增加了碳原子分布有序度。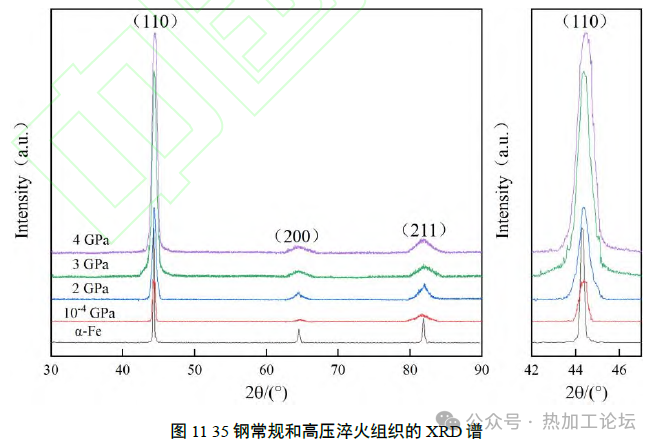

由35 钢常规和高压淬火组织的XRD 图可知,在2~4 GPa 高压下淬火时衍射峰半高宽(FWHM)较常规淬火有所宽展,且宽展度随淬火压力升高而增大,表明高压淬火马氏体组织更细、缺陷密度更高。采用WilliamsonHall(WH)方法估算了不同淬火压力下35 钢淬火组织中的位错密度,对每个压力淬火的试验合金都进行了3个样品的XRD测试,取平均值进行估算。经计算,常规淬火马氏体的位错密度为3.12×1015m-2,2、3 和4GPa 淬火马氏体的位错密度分别为8.75×1015m-2、9.84×1015m-2和1.07×1016m-2,即位错密度随淬火压力的升高逐渐增大。 由此可见,高压淬火不但能细化马氏体组织、提高组织中缺陷密度,还提高了M2 型马氏体所占比例(或降低M3 型马氏体所占比例),提高了马氏体晶格正方度,即增加了碳原子分布有序度。2.3 淬火压力对35 钢力学性能的影响及力学性能提升机制 图12所示为不同压力下淬火的35 钢的力学性能。由图12(a)可知,常规淬火(经860 ℃×20 min 奥氏体化,水淬)35 钢硬度为512HV,2、3 GPa 淬火(860 ℃×20 min 奥氏体化,保压下以6 ℃/s 冷却)35钢硬度分别为743HV 和807HV,较常规淬火分别提高45%和57%。4 GPa 淬火35 钢硬度高达832HV,较常规淬火大幅提高(63%)。此外,3 GPa 淬火35 钢硬度较2 GPa 提高8.6%,而4 GPa 淬火35 钢硬度较3GPa 提高3.1%。因此在GPa 级高压下淬火,35 钢硬度并不随压力提高线性升高。 淬火态35 钢的硬度主要取决于马氏体硬度及残余奥氏体量。由穆斯堡尔测试结果可知,35 钢组织中的残余奥氏体量与常规淬火相近,因而高压淬火35 钢硬度的提升主要取决于高压淬火马氏体硬度。正方结构马氏体中间隙位置为扁八面体,长轴间隙半径0.079 nm,短轴间隙半径0.020 nm;高压淬火后,马氏体晶格常数a 由常规淬火的0.287 nm 减小到4 GPa 淬火下的0.284 nm,扁八面体间隙半径(短轴)由常规淬火下的0.020 nm 减小到4 GPa 下的0.017 nm。原子半径为0.077 nm 的碳原子处于八面体间隙后,形成以碳原子为中心的晶格畸变偶极应力场。该应力场与位错产生强烈的交互作用,是马氏体强硬度提升的主导因素,故马氏体硬度主要取决于碳固溶量。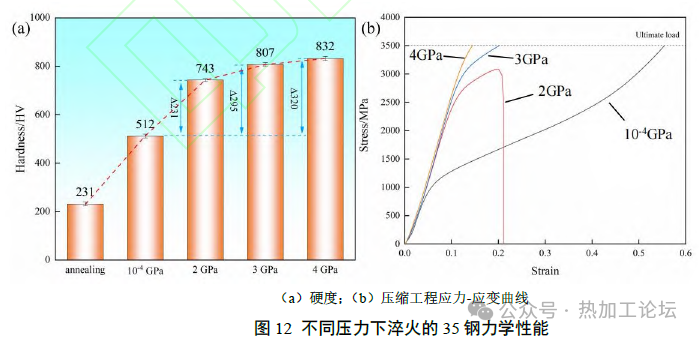
从上述试验结果可知,在2、3 GPa 淬火组织与常规淬火组织中均未观察到碳化物相,表明碳原子多固溶于马氏体中。2、3GPa 下淬火时扁八面体间隙半径(短轴)的减小(固溶碳量相同),晶格畸变偶畸应力场变大,导致2、3GPa 淬火35 钢的硬度较常规淬火马氏体分别提高45%和57%。而在4GPa 下淬火时,虽然扁八面体间隙半径(短轴)较3 GPa 更小,但4 GPa 淬火35 钢硬度较3GPa 淬火35 钢仅增加3.1%。高压淬火下碳原子分布有序度提高,且M3型(第三亚点阵)马氏体所占比例下降,也可能是2~4GPa 淬火35 钢硬度提升幅度减小的原因。 由图12(b)可知,常规淬火35 钢压缩屈服强度为1.08 GPa,因35 钢具有良好的塑性,在本压缩试验条件下未被压断,故没有测出压缩率。2 GPa 淬火35 钢压缩屈服强度达到2.63 GPa,较常规淬火提高143%;但塑性较低,压缩率仅有22%。3GPa 和4GPa 淬火35 钢的屈服强度更是高达2.97GPa 和3.35GPa,但是由于受设备所限,没有测到抗压强度和压缩率。可见,高压淬火极大地高了35 钢的硬度和压缩屈服强度,4GPa 淬火35 钢的硬度高达832HV,压缩屈服强度超过3.0GPa,且具有一定的塑性。 位错强化、碳固溶强化、细晶强化及时效强化是淬火钢强度提升的主要机制。有证据表明,Fe-C马氏体的强化主要是由位错和晶界结构引起的,而碳过饱和对强度的贡献小于总强度的10%。因此将着重计算位错强化和细晶强化对屈服强度的贡献,把额外的强度提升归因于过饱和碳的固溶强化以及孪晶界的增多。 位错密度与材料强度之间的关系一般可用Bailey-Hirsch 公式进行定量分析。 式中:??为材料位错强化后的屈服强度,MPa;??0为由其他因素造成位错运动的阻力,MPa;α 为系数,对于多晶铁素体α=0.4,μ为剪切模量,b 为伯格斯矢量的值,α、μ、b 均为与材料性质有关的常数;ρ 为材料的位错密度,m-2。 根据式(2)可知,材料的屈服强度与位错密度的平方根成正比关系。在此基础上,TAKAKI S为计算位错强化对材料强度的贡献,提出了新的Bailey-Hirsch 公式。 式中:Δ??为位错强化带来的屈服强度提升值,MPa;ρX-ray为由XRD 计算所得的位错密度,m-2。 将依据XRD谱计算得到的常规及2、3、4 GPa 淬火35 钢的位错密度分别代入式(3),求得位错强化对屈服强度贡献值。位错强化对常规淬火35 钢屈服强度贡献值为670.3 MPa,贡献了屈服强度的62.1%。 位错强化对2、3 和4GPa 淬火35钢屈服强度贡献值分别为1122.5、1190.4、1241.3 MPa,分别贡献了屈服强度的42.7%、40.1%和37.1%。此外,由上述试验结果可知,高压淬火极大地细化了马氏体板条,使马氏体板条厚度由常规淬火的500 nm细化到2、3 和4GPa 淬火的30、20、14 nm。WANG C F 等研究板条马氏体微观组织与力学性能相关性时发现,马氏体屈服强度与Block 板条宽度符合Hall-Patch 关系。为此,依据式(4)的Hall-Patch 公式计算了马氏体板条细化对压缩屈服强度的贡献率。计算结果显示,细晶强化对常规淬火35 钢屈服强度贡献值为282.8 MPa,贡献值比例为26.2%。细晶强化对2、3 和4GPa 淬火35钢屈服强度贡献值分别为1154.7、1414.2、1690.3 MPa,贡献值比例分别为43.9%、47.6%和50.5%。 式中:σ?????为细晶强化对强度的贡献,MPa;???????为Hall-Patch 因子,取0.2 GPa?μm1/2;??为马氏体板条束等效尺寸,μm。 图13 所示为不同压力下各强化机制对35 钢压缩屈服强度的贡献率。由图12 可知,常规淬火下,位错强化对屈服强度的贡献率(62.1%)明显高于马氏体板条细化引起的细晶强化(26.2%),即位错强化是常规淬火35 钢最重要的强化机制。而高压下淬火时马氏体板条细化所产生的细晶强化对屈服强度的贡献率随淬火压力升高而增大,4GPa 淬火时细晶强化贡献率(50.5%)远高于位错强化效应(37.1%)。可见,高压淬火改变了马氏体各强化机制贡献次序,马氏体板条细化所产生的细晶强化对屈服强度的贡献率超过位错强化,成为最主要的强化机制。再者,高压下淬火时过饱和碳的固溶强化、片状马氏体含量增多,以及60°[111]孪晶界增多等也对屈服强度提升有一定的贡献。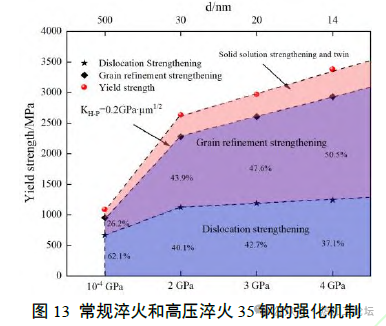
1)与常规淬火35 钢的马氏体相比,2~4GPa 淬火35 钢中马氏体板条束结构和马氏体片特征更为明显,且马氏体板条尺寸显著细化,由常规淬火下的500 nm 细化至4GPa 下的14 nm。高压淬火组织中缺陷密度大幅提升,尤其是60°[111]孪晶界所占比例由常规淬火6%提高到4GPa 淬火的26%,显示马氏体相变机制发生改变。2)35 钢淬火马氏体晶格常数a 和c 由常规淬火下0.287 nm 和0.289 nm 减小到4GPa 下的0.284 nm 和0.288 nm,正方度c/a 由常规淬火下的1.009 增大到4GPa 下的1.014。高压淬火马氏体中,M2 型马氏体所占比例高于常规淬火,由常规淬火的63.59%增加至4GPa 淬火的72.93%;M3 型马氏体所占比例低于常规淬火,由常规淬火的34.35%降低至4GPa 淬火的24.60%。即高压淬火提高了马氏体中碳原子分布有序度,并降低第3 类亚点阵所占比例。3)2、3 和4GPa 压力下淬火35 钢的硬度分别为743HV、807HV 和832HV,较常规淬火(512HV)分别提高45%、58%和63%。2GPa 淬火的35 钢压缩屈服强度为2.63GPa,较常规淬火(1.08 GPa)提高了143%;尤其4 GPa 淬火的35 钢,其压缩屈服强度达到了3.35 GPa,是常规淬火的3 倍以上。其中,高压下马氏体晶格常数减小导致的碳原子间隙固溶造成的晶格畸变程度加大,板条束尺寸大幅细化所导致的细晶强化以及相变过程中产生的位错和孪晶界密度的显著增加是其强化的主要机制。
来源:热加工论坛
点我访问原文链接