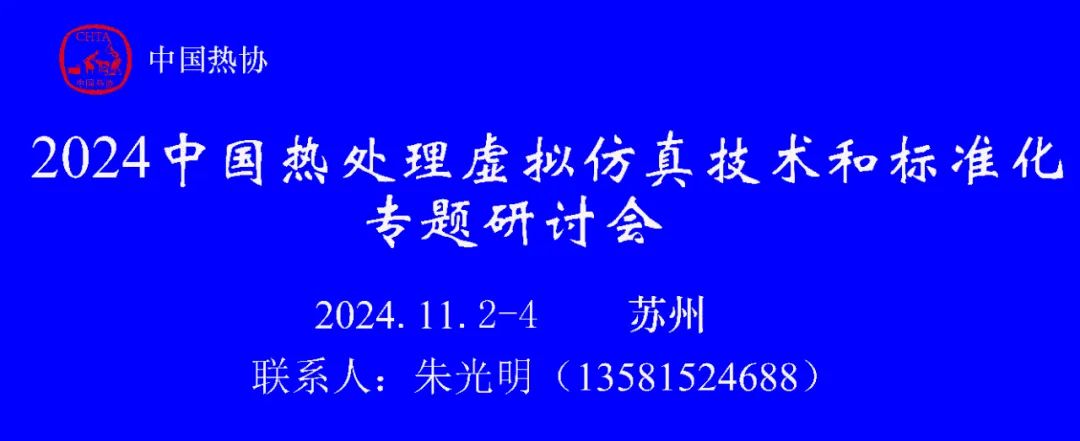
风电齿轮钢用于风力发电机的机械传动,要求其具有很高的耐疲劳性能,因此对其内部质量要求很高。超声波探伤是检测风电齿轮钢内部缺陷的主要方法之一。近年来,随着各大风电厂主机厂不断提质降本,对风电齿轮的探伤要求越来越高,部分产品功能区探伤缺陷平底孔当量提高至约Φ0.38mm,随之而来对齿轮钢材的洁净度也提出了更高的要求。国内某钢厂材料生产的风电齿轮按此要求探伤的缺陷率存在不稳定问题,部分炉次超声探伤缺陷率甚至超过10%,产品质量风险较大,亟需解决。 超声波探伤是一种广泛运用于材料内部无损检测的手段,可以检测出裂纹、孔洞、大尺寸夹杂物等与基体差别较大的介质。导致探伤缺陷的原因很多,而对于大型锻件而言,大尺寸夹杂物是其主要形成原因之一。代卫星等研究了N08811耐蚀合金管坯探伤缺陷的成因,指出探伤缺陷是由高熔点Al2O3-MgO-TiOx 氧化物与TiN 组成的复合大尺寸团簇夹杂物组成。张威风等研究了Cr5 大型锻钢轧辊探伤缺陷的形成与控制,指出探伤缺陷是单个大尺寸SiO2-MnO-Al2O3 夹杂物导致,而SiO2-MnO-Al2O3 夹杂物的出现和钢液[Al]含量有关。石如星等研究了16Mn 钢空心锻件的探伤缺陷形成原因,结果表明,缺陷是由MnO-SiO2-Al2O3-CaO、Al2O3-MgO-ZrO2-CaO 和SiO2-Al2O3-ZrO2 类夹杂物聚集而成。虽然夹杂物导致缺陷方面的研究陆续有报道,但不同钢种的缺陷夹杂物类型有很大差异,这与冶炼工艺差异有关。因此,不同钢种以及不同工况下夹杂物缺陷的种类和形成原因也存在差异。目前针对风电齿轮钢大尺寸探伤缺陷的研究还很少,现场探伤缺陷问题的改进缺少理论参考。 笔者围绕风电齿轮钢中的大尺寸探伤缺陷问题,首先通过对缺陷查找和观察,明确缺陷的类型和特征。再通过精炼过程取样,得出大尺寸缺陷夹杂物的形成阶段。最后,结合热力学计算,得出大尺寸缺陷夹杂物在精炼过程的形成与演变行为。本研究最终阐明风电齿轮钢中大尺寸探伤缺陷的形成机理,并提出了工艺改进建议。
试验样品均为客户反馈的不合格产品,风电齿轮钢的化学成分见表1。首先对样品进行缺陷复检定位,运用手持数字式超声波探伤仪(TUB100)对缺陷进行初步定位,可以将缺陷的位置确定在10mm 范围内;再用超声波扫描显微镜(PVA301)对缺陷进行精确定位,可以将缺陷的位置确定在1mm 范围内。接着运用扫描电子显微镜和能谱分析仪(MLA250)对找到的缺陷进行形貌观察和成分检测。

为了查找缺陷的形成原因,对风电齿轮钢精炼过程进行过程取样。风电齿轮钢的精炼流程、部分关键工艺和取样方案如图1所示,精炼过程为:电炉-LF-VD-CC,取样工艺环节依次为:LF到站(样1),该样是在钢包进LF 工位后取得;LF 初样(样2),该样是在LF第1 次通电升温化渣完毕后取得;LF过程样(样3),该样是在LF 合金化基本完成后取得;LF出站(样4),该样是在LF 精炼完成后出站之前取得;VD破空后(样5),该样是在VD破空后立即取得;软吹10min(样6),该样是在VD 破空后的软吹10min后取得;VD吊包前(样7),该样是在软吹完成后吊包上连铸平台之前取得;中间包(样8),该样是在钢包浇注一半时的中间包浇注区取得。采用直读光谱仪(ARL8860)对取样样品的钢液成分进行检测,再利用X 射线荧光光谱仪对样5 对应的炉渣成分进行检测,最后运用商业软件FactSage 8.2 对夹杂物的形成进行热力学计算。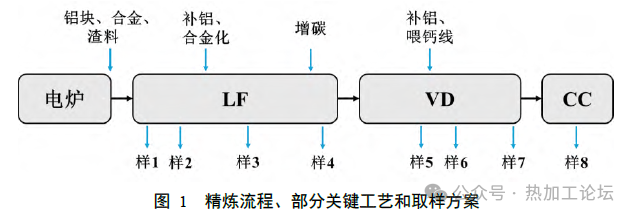
通过超声波扫描显微镜对缺陷进行精确定位,缺陷数据包含许多同类型缺陷,其中典型的检测结果如图2 所示。图2(a)所示为俯视透视图,图中亮斑即为缺陷,其中有两个较大尺寸的缺陷和较多数量的小尺寸缺陷。图2(a)上半部分出现一块纯黑色区域,其为取样后留下的空洞,对检测结果没有影响。图2(b)所示为最大尺寸缺陷的侧视透视图,图中上下两条光亮带是样品的上下表面。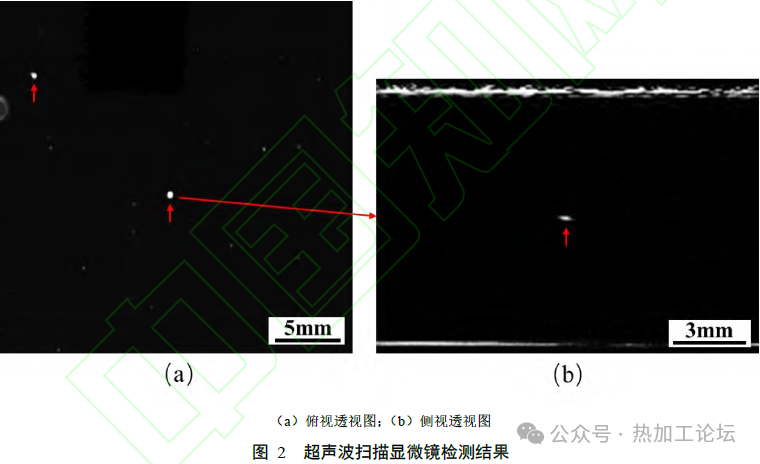
通过精确定位可以发现这些缺陷是大尺寸夹杂物,如图3 所示。图3 所示为部分夹杂物的能谱面扫描结果,从图中可以看出,这些夹杂物呈不规则形状,观察面上的尺寸为30~100μm。由于磨样只能观察到缺陷的1 个截面,而这个截面体现不出缺陷的总体形貌,所以实际观察结果比检测结果偏小。大尺寸夹杂物呈不均匀状态,由MgO-Al2O3、CaO-MgO-Al2O3-SiO2 组成,外围附着少量CaS。图4 所示为部分夹杂物的能谱点扫描结果,图中数字表示原子数分数。结果显示,MgO-Al2O3 中的Al、Mg 原子比接近2:1,CaOMgO-Al2O3-SiO2 中的Ca、Al 比接近1:1。通过能谱点扫描进一步确认大尺寸缺陷夹杂物是由黑色的MgOAl2O3和灰色的CaO-MgO-Al2O3-SiO2 组成。夹杂物中有较高含量的Si 元素,这在铝脱氧钢中并不常见。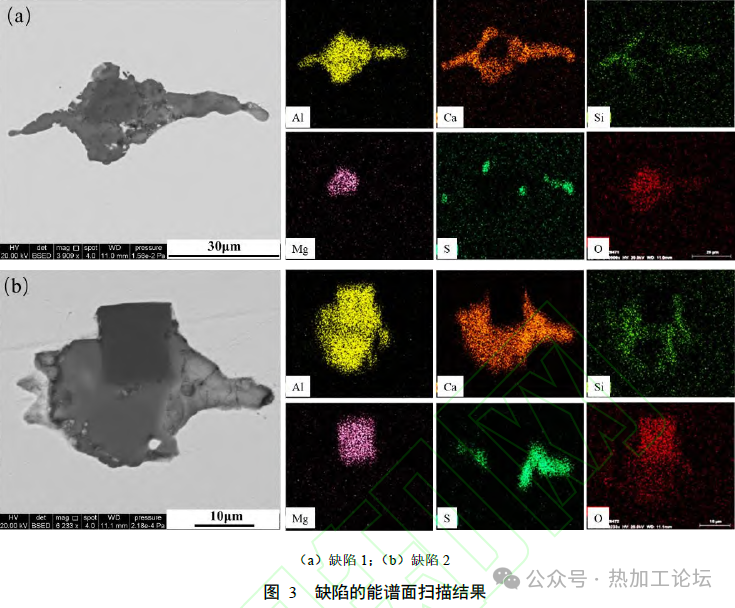
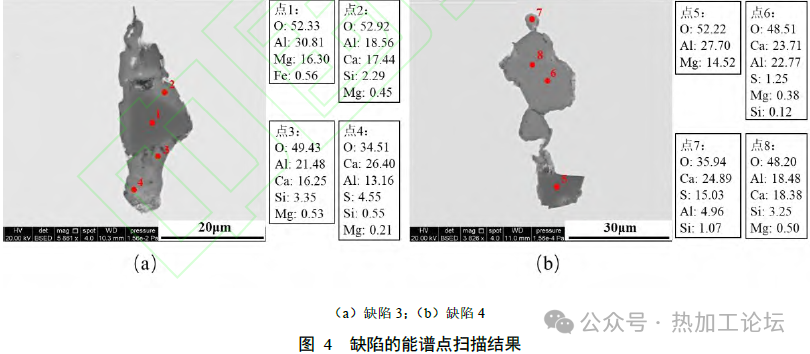
由于这些大尺寸夹杂物不均匀,在每个夹杂物上进行多点检测,然后将所有点成分放入三元相图中,得到如图5 所示结果。图5 所示为运用FactSage 8.2 计算得到的1600℃的三元相图,其中图5(a)所示为CaO-MgO-Al2O3 相图,图5(b)所示为CaO-SiO2-Al2O3 相图。从图中可以看出,缺陷夹杂物主要由液态的高钙CaO-MgO-Al2O3-SiO2 氧化物和固态的无钙镁铝尖晶石组成,而液态CaO-MgO-Al2O3-SiO2 氧化物中的SiO2 质量分数为0~12%。通过相图分析,进一步确认了大尺寸缺陷夹杂物的组成,从形貌和组成上看,这些大尺寸夹杂物缺陷是由不同种类的多个较小尺寸夹杂物聚集而成,从而使得大尺寸夹杂物呈现不规则形貌。
从形貌和组成上看,缺陷夹杂物是由多个不同类型的夹杂物聚集而成,这些夹杂物主要为MgO-Al2O3、CaO-MgO-Al2O3-SiO2 和少量CaS。本研究钢种中S 的质量分数小于0.01%,因此CaS 不会在冶炼过程中出现,只在凝固降温过程中形成,从而出现在缺陷夹杂物的外围。MgO-Al2O3 主要以镁铝尖晶石形态存在,是铝脱氧钢中的常见夹杂物,因此,大尺寸缺陷夹杂物的主体特征是CaO-MgO-Al2O3-SiO2。笔者以CaO-MgO-Al2O3-SiO2 夹杂物为主线,着重探究CaO-MgO-Al2O3-SiO2 夹杂物的形成机理,从而得出大尺寸缺陷夹杂物的出现原因,最终提出抑制该缺陷的措施。 缺陷夹杂物以氧化物为主,而大尺寸氧化物基本来源于精炼过程。因此,为了查找缺陷夹杂物在精炼过程的形成工艺阶段,对风电齿轮钢精炼过程进行过程取样分析,包括钢液成分、炉渣成分和夹杂物成分。 图6 所示为风电齿轮钢精炼过程的夹杂物三元相图,1个圆球表示1 个夹杂物,球的大小表示夹杂物尺寸。图6(a)所示为是CaO-MgO-Al2O3 类三元相图,包括含Si 和不含Si 的所有CaO-MgO-Al2O3 夹杂物。从图中可以看出,LF 到站时主要为Al2O3;随后[Mg]进入夹杂物中,形成MgO-Al2O3 和CaO-MgOAl2O3,夹杂物成分逐渐向镁铝尖晶石方向移动;LF 中后期,夹杂物主要集中在镁铝尖晶石附近;VD 真空搅拌后夹杂物成分向高钙液相区移动,VD破空后基本为液态夹杂物。整体来看,冶炼过程中的夹杂物主要在3个位置聚集:Al2O3、镁铝尖晶石、高钙液相区,其中高钙液相区内的夹杂物尺寸较大。 图6(b)所示为含Si 的CaO-MgO-Al2O3 夹杂物在CaO-SiO2-Al2O3 三元相图中的分布情况,主要研究夹杂物中SiO2 含量的变化。相图显示,LF 过程基本没有含Si 夹杂物出现,而在VD 破空后,含Si 夹杂物大量出现,几乎所有CaO-MgO-Al2O3 夹杂物里面均含有Si。含Si 的CaO-MgO-Al2O3 夹杂物在VD 破空后大量出现,后期一直以液态形式存在于钢液中。显然,这些含Si 的CaO-MgO-Al2O3 夹杂物是可能的缺陷夹杂物来源。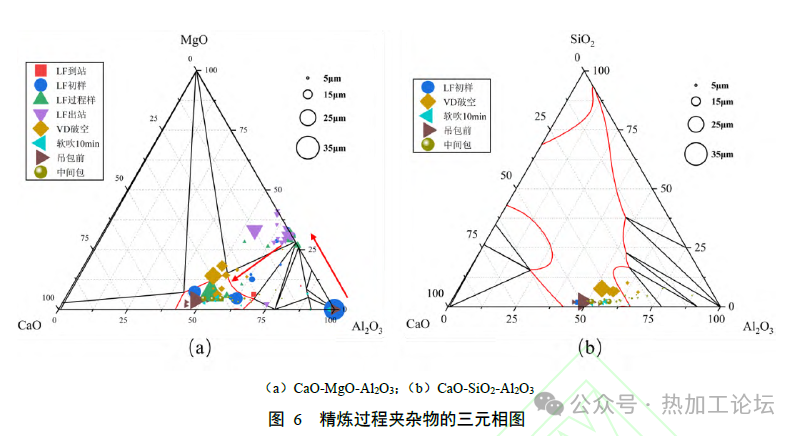
为了进一步确认缺陷夹杂物的形成工艺阶段,对精炼过程中含SiCaO-MgO-Al2O3 夹杂物的变化情况进行分析统计,结果如图7 所示。图7(a)所示为冶炼过程的夹杂物尺寸情况。显然,LF 过程几乎没有含Si 的CaO-MgO-Al2O3 夹杂物出现,而该夹杂物在VD 破空后大量出现,且到中间包也一直存在。这些夹杂物的尺寸有大有小,在25μm以下均有存在。图7(a)结果进一步确认含Si 的CaO-MgO-Al2O3 夹杂物是在VD 过程出现,且后期一直存在。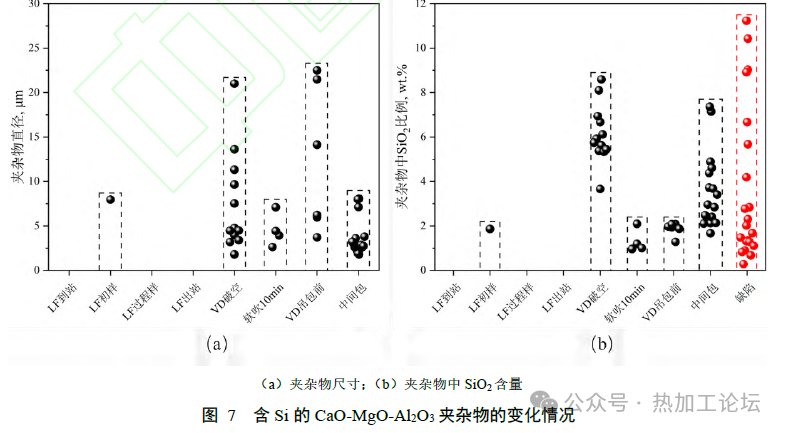
图7(b)所示为冶炼过程中含Si 的CaO-MgO-Al2O3 夹杂物中SiO2 含量与缺陷中SiO2 含量的比较。 结果显示,VD破空后的SiO2 质量分数为5%~10%,与缺陷中的SiO2 质量分数接近。软吹和吊包前的样品中高含量SiO2 夹杂物减少,中间包中高含量SiO2 夹杂物再次增多,和缺陷中SiO2 质量分数接近。这种变化情况与钢液混匀程度、夹杂物演变有关。通过夹杂物中的SiO2 含量比较,可以明确缺陷中的CaO-MgOAl2O3-SiO2 夹杂物源自精炼过程高SiO2 含量的CaO-MgO-Al2O3 夹杂物。也就是说,缺陷中的CaO-MgOAl2O3-SiO2 夹杂物是在VD 过程中出现的。 上述讨论发现,精炼过程的夹杂物变化很大。LF 到站时主要是Al2O3,随后变为MgO-Al2O3 和CaOMgO-Al2O3,LF 中后期的夹杂物主要集中在镁铝尖晶石附近;VD 破空后基本为含Si 的CaO-MgO-Al2O3夹杂物,这些夹杂物一直保留在钢液中。而缺陷夹杂物CaO-MgO-Al2O3-SiO2 即源自精炼过程含Si 的CaOMgO-Al2O3 夹杂物。通过精炼过程的夹杂物分析,最终发现缺陷夹杂物CaO-MgO-Al2O3-SiO2 是在VD 真空处理过程出现。 VD 工艺是真空大搅拌过程,钢液和炉渣充分接触,很多研究发现这个过程存在卷渣现象,从而导致炉渣以夹杂物的形式进入钢液。为了明确缺陷夹杂物CaO-MgO-Al2O3-SiO2 是否为卷渣导致的,将破空时的夹杂物成分与炉渣成分进行对比,得到如图8 所示结果。图中结果显示,破空夹杂物中的MgO 平均质量分数为10.7%,炉渣中的MgO 质量分数为8.1%,夹杂物中的MgO 偏高;夹杂物中Al2O3 平均质量分数为50.0%,炉渣中Al2O3质量分数为26.7%,夹杂物中Al2O3 远高于炉渣;夹杂物中SiO2 平均质量分数为6.4%,炉渣中SiO2 质量分数为13.4%,夹杂物中SiO2 偏低;夹杂物中CaO 平均质量分数为32.9%,炉渣中CaO 质量分数为51.7%,夹杂物中CaO 远低于炉渣。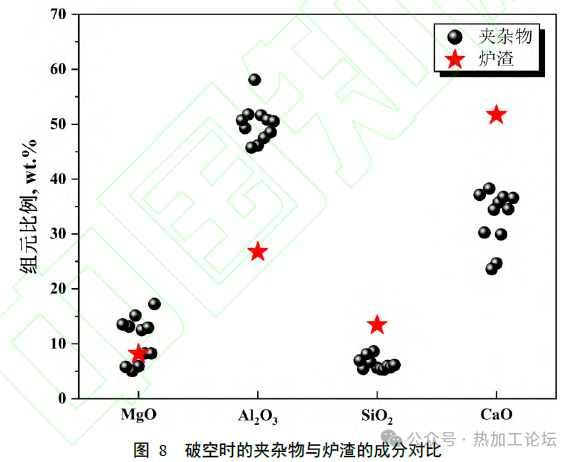
通过破空时夹杂物与炉渣组成比较发现,虽然夹杂物中的MgO 含量与炉渣接近,但夹杂物中的Al2O3含量远高于炉渣,而SiO2 含量和CaO 含量比炉渣中的低很多,说明破空后的夹杂物组成与破空后的炉渣成分不一致。从夹杂物和炉渣组成上看,破空后钢液中的CaO-MgO-Al2O3-SiO2 夹杂物不是卷渣所导致的;从夹杂物的成分上看,LF 过程的所有CaO-MgO-Al2O3 夹杂物都不含Si,而VD 破空后的所有CaO-MgOAl2O3夹杂物都含Si,同样可知其不是卷渣能导致的。卷渣只能增加新的夹杂物类型,而不能改变之前已经存在的夹杂物。综上可知,卷渣不是导致VD破空后大量CaO-MgO-Al2O3-SiO2 夹杂物出现的原因。 在VD过程中,钢液和炉渣充分接触反应,钢液的成分会发生一定变化,特别是脱氧元素Al 的变化很大,可改变夹杂物的平衡状态。因此,进一步对钢液成分和炉渣成分进行了梳理。冶炼过程的钢液成分见表2。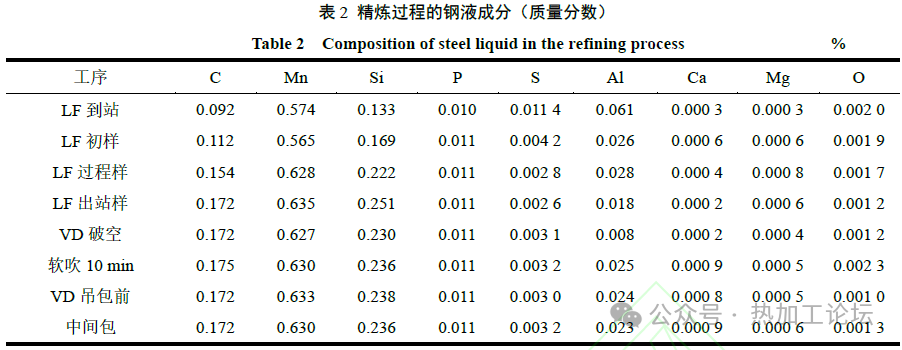
VD 过程中,钢液中[Al]质量分数从0.018%降低至0.008%,破空后进行补铝操作,[Al]质量分数升至0.025%,中间包中的[Al]质量分数稳定在0.023%;破空后进行喂钙线操作,[Ca]质量分数从0.0002%升至0.0009%,中间包中的[Ca]质量分数稳定在0.0009%。 为了得出钢液成分变化对夹杂物的影响,基于破空时的钢液成分,运用热力学软件FactSage 8.2 计算得出平衡状态下的夹杂物情况,结果如图9 所示。图9 所示为风电齿轮钢中的夹杂物平衡相图,存在3个平衡态区:固态镁铝尖晶石区(MA)、液态夹杂物+固态镁铝尖晶石区(L+MA)、液态夹杂物区(L)。VD破空后,[Al]质量分数为0.008%,[Ca]质量分数为0.0002%,钢液中的平衡态夹杂物为液态夹杂物和固态镁铝尖晶石。后期补铝线和钙线后,钢液中[Ca]质量分数升至0.0009%,[Al]质量分数升至0.023%,钢液中的平衡态夹杂物也变为纯液态夹杂物,这和冶炼过程的夹杂物变化规律一致。由于VD 后期钢液中[Ca]含量增高,镁铝尖晶石会被改性为高Ca 的液态夹杂物,但仍然存在未完全改性的残留镁铝尖晶石。另一方面,凝固降温过程中液态夹杂物内部、钢液中都会析出固态镁铝尖晶石,这些都有可能是大尺寸缺陷夹杂物中镁铝尖晶石的来源。但大尺寸缺陷夹杂物的主体是CaO-MgO-Al2O3-SiO2 夹杂物,因此这里不对镁铝尖晶石的来源作过多研究。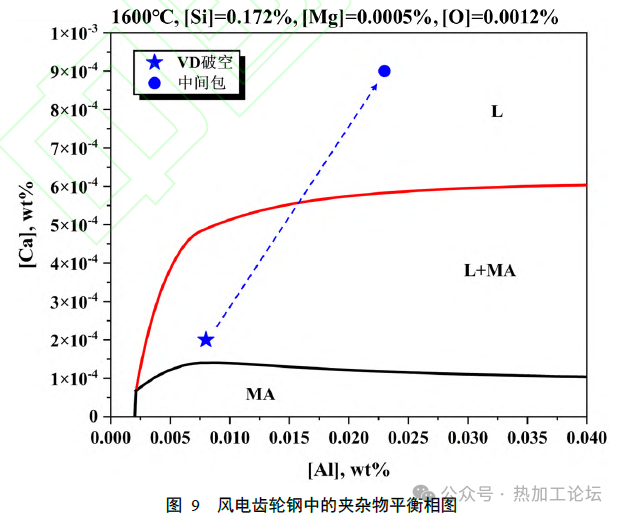
因为CaO-MgO-Al2O3-SiO2 夹杂物都是液态夹杂物,进一步对图9 中的液态夹杂物(L)组元变化进行计算分析,图10 所示为液态夹杂物的组元平衡相图。参考VD 破空后的钢液成分,设定[Ca]质量分数为定值0.0002%。由图10 可见,随着钢液中[Al]含量的变化,液态夹杂物中的组元比例变化显著。分别将VD破空后和中间包中的CaO-MgO-Al2O3-SiO2 夹杂物放入平衡相图发现,VD 破空后钢液中[Al]质量分数为0.008%,此时CaO-MgO-Al2O3-SiO2 夹杂物组成与平衡态基本一致;当进行连铸时,中间包[Al]质量分数稳定在0.023%,此时CaO-MgO-Al2O3-SiO2 夹杂物组成也与平衡态基本一致。中间包 [Ca]质量分数为0.0009%,比计算设定值大,因此中间包夹杂物中CaO 含量下降不明显。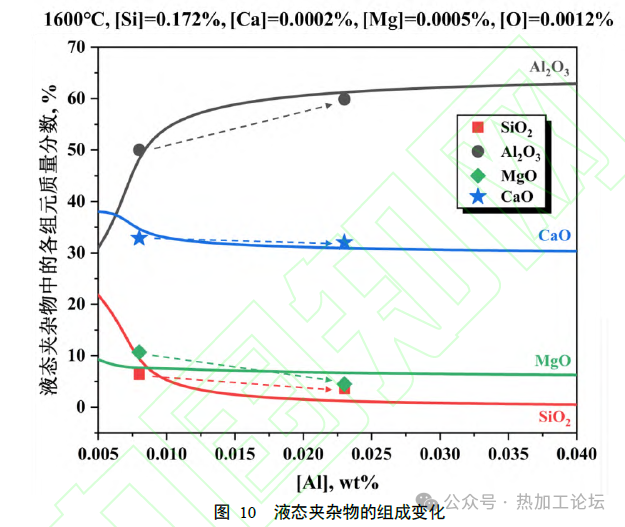
通过热力学计算发现,VD 过程夹杂物变化与热力学平衡态的变化一致。也就是说,CaO-MgO-Al2O3-SiO2 夹杂物的形成和变化是由钢液成分变化导致的,且主要是钢液中[Al]含量的变化导致。综上可知,缺陷夹杂物CaO-MgO-Al2O3-SiO2 在VD 过程的出现是由钢液中[Al]含量过低导致的,且后期随着[Al]含量的升高进一步变化。 VD 过程中,钢液中的[Al]发生大程度烧损,夹杂物向着[Al]含量降低的方向转变。当[Al]质量分数低于0.010%时,Al 不再是主要的脱氧元素,Si 元素的作用逐渐显现,钢液与夹杂物发生如式(1)所示反应:
钢液中的[Si]会将CaO-MgO-Al2O3 夹杂物中的部分Al2O3 还原,最终导致钢液中的[Si]进入夹杂物中,形成高SiO2 含量的CaO-MgO-Al2O3-SiO2 夹杂物。由于Al 和O 的结合能力减弱,夹杂物中的MgO、CaO含量也会小幅度升高,但都没有SiO2 含量的变化显著。 VD 破空后,会立即采取补铝和喂钙线的操作。钢液中的[Al]质量分数升高至0.024%左右,夹杂物成分向[Al]含量升高的方向移动。当[Al]质量分数高于0.010%时,Al 重新成为主要脱氧元素,Si 元素的作用逐渐降低,钢液与夹杂物主要发生如式(2)所示反应:
夹杂物中部分SiO2 会被[Al]还原,使得CaO-MgO-Al2O3-SiO2 夹杂物中SiO2 比例降低,这即为图7(b)中夹杂物SiO2含量在软吹10 min 和吊包前降低的主要原因。由于Al 和O 的结合能力增加,夹杂物中MgO、CaO 含量也会小幅度降低,但没有SiO2 含量的变化显著。 综上可知,大尺寸缺陷夹杂物实际上源自VD 过程生成的高SiO2 含量CaO-MgO-Al2O3-SiO2 夹杂物。 该夹杂物是由VD 过程钢液[Al]大量烧损后过低导致的。钢液中的[Si]将夹杂物中的Al2O3 还原,进入夹杂物。由于VD 过程搅拌剧烈、动力学充足而使得破空后的所有CaO-MgO-Al2O3-SiO2 夹杂物的SiO2 含量均很高,如图7(b)所示。VD 补铝后,夹杂物中的SiO2 含量有所降低,因此夹杂物中的SiO2 含量在软吹10 min 和吊包前降低,如图7(b)所示。实际上,虽然VD 补铝后的夹杂物中SiO2 含量会降低,但动力学不充足,仍然会有一定量的高SiO2 含量CaO-MgO-Al2O3-SiO2 夹杂物存在。从钢包到中间包,钢液重新混匀后,这些残余的高SiO2 含量CaO-MgO-Al2O3-SiO2 夹杂物重新被检测到,如图7(b)所示。因此,中间包CaO-MgO-Al2O3-SiO2 夹杂物的SiO2 含量呈现出有高有低的状态,而不是单一的高SiO2 含量,中间包内夹杂物状态和缺陷夹杂物一致。 风电齿轮钢中的大尺寸缺陷夹杂物是由镁铝尖晶石和CaO-MgO-Al2O3-SiO2 夹杂物聚集而成,其中CaO-MgO-Al2O3-SiO2 夹杂物为主体。而缺陷中的CaO-MgO-Al2O3-SiO2 夹杂物源自钢液在VD 过程形成的高SiO2 含量CaO-MgO-Al2O3-SiO2 夹杂物,VD 过程过低的[Al]含量是该夹杂物形成的根本原因。因此,要想减少这类大尺寸缺陷夹杂物的出现,提高VD过程钢液中的[Al]含量是关键。VD 破空后的[Al]质量分数应大于0.01%,接近0.015%为宜。另外,VD 破空后补加钙线同样会使钢液中出现大量的高钙液态夹杂物,该夹杂物尺寸大且不容易上浮去除,凝固降温过程中会扮演CaO-MgO-Al2O3-SiO2 夹杂物的角色,导致大尺寸夹杂物出现。因此,VD破空后的喂钙线操作须慎重考虑。
1)风电齿轮钢中的探伤缺陷实际上是大尺寸夹杂物。这种缺陷夹杂物是由固态的镁铝尖晶石和液态的CaO-MgO-Al2O3-SiO2 夹杂物聚集而成,外围附着少量CaS。缺陷夹杂物主体是CaO-MgO-Al2O3-SiO2 夹杂物。
2)缺陷中的CaO-MgO-Al2O3-SiO2 夹杂物源自VD 过程产生的高SiO2 含量CaO-MgO-Al2O3-SiO2 夹杂物,夹杂物中的高SiO2 含量是其主要特征。3)VD 过程钢液中过低的[Al]含量是高SiO2 含量CaO-MgO-Al2O3-SiO2 夹杂物形成的根本原因。由于[Al]含量过低,钢液中的[Si]将夹杂物中的Al2O3 还原,形成高SiO2 含量CaO-MgO-Al2O3-SiO2 夹杂物。随着钢液中[Al]含量重新升高,夹杂物中的SiO2被部分还原,但仍然有高SiO2 含量的CaO-MgO-Al2O3-SiO2夹杂物残留。
来源:热加工论坛
点我访问原文链接